
As p8ntballers, we put a lot of faith in our equipment.
we throw ourselves into bunkers or trees and dive over lanes of paint / through bushes with little regard to the effect it has on our equipment. a lot of the time, we will just assume that its going to work out OK on the other side.
I recently had some bottles tested and ended up talking to the guys that did it, they were willing to show me behind the curtain.
Whilst there, I figured it may be more than just me who was interested in what goes on to test one of the most dangerous pieces of kit we carry with us.
So here we go, a short step by step of what happens!
1. Get cleaned up.
Any stickers /covers / tape has to be removed before a visual inspection to the outside of the cylinder is performed, the tester is looking for any chips / cracks in the fibre wrapping as any over 2mm deep will cause the bottle to fail it's testing.
2. Internal visual inspection
A light is fed into the bottle, and it is checked any signs of rust, rust inside the bottle would signify that liquid had somehow made its way inside, this can be rectified with a high pressure shot blasting tool which fires small metal beads out of a nozzle to abrasively clean the area.
3. Test the threads
The internal threads of the bottle are then tested to make sure they have not worn excessively.
This is done using a tool which has a sharp thread end, and a flattened thread end. The sharp end should thread snugly into the bottle, whilst the flattened end should not manage to make its way down the threads of the bottle, if that happens it indicates that the threads have worn and are no longer suitable for gripping onto the regulator thread.
4. Fill 'er up!
The part we all know is coming, high pressure testing, but why are you putting water in my AIR bottle?!
Well, water wont compress anywhere near as much as air will, so, if there is a failure in the bottle under pressure, there won't be a massive purge of all the pressure that is being held. So that is a significant amount safer.
Our bottle gets filled via funnel to start (to make sure there is no air left inside) and then the hose is bolted on to the bottle via the regulator threads. At this point, i'm excited, a thick screen gets wheeled in-front of the bottle, and away we go, 4500 psi of water is loaded into the bottle. No problem, I've put that much air in there before, I'm confident.
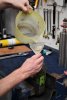
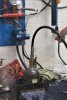
The bottle is checked for leaks, any sign of water making its way out of the bottle at this point would indicate an issue that would also happen with air.
The bottle is dry and the testing continues, it's at this point I start to get a little nervous, 6500 psi of water is loaded into the bottle. That is a lot of pressure!
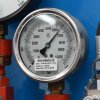
Fortunately for me, this bottle (like the majority of others) happily passes its testing, it is issued with another cycle of safety certificate (which takes this one up to its death date) and I am sent on my way.
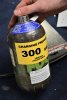
Many thanks to the guys over at Obsequio in Hampshire for spending the time with me, and for letting me jot down how it all happens.
we throw ourselves into bunkers or trees and dive over lanes of paint / through bushes with little regard to the effect it has on our equipment. a lot of the time, we will just assume that its going to work out OK on the other side.
I recently had some bottles tested and ended up talking to the guys that did it, they were willing to show me behind the curtain.
Whilst there, I figured it may be more than just me who was interested in what goes on to test one of the most dangerous pieces of kit we carry with us.
So here we go, a short step by step of what happens!
1. Get cleaned up.
Any stickers /covers / tape has to be removed before a visual inspection to the outside of the cylinder is performed, the tester is looking for any chips / cracks in the fibre wrapping as any over 2mm deep will cause the bottle to fail it's testing.
2. Internal visual inspection
A light is fed into the bottle, and it is checked any signs of rust, rust inside the bottle would signify that liquid had somehow made its way inside, this can be rectified with a high pressure shot blasting tool which fires small metal beads out of a nozzle to abrasively clean the area.
3. Test the threads
The internal threads of the bottle are then tested to make sure they have not worn excessively.
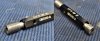
This is done using a tool which has a sharp thread end, and a flattened thread end. The sharp end should thread snugly into the bottle, whilst the flattened end should not manage to make its way down the threads of the bottle, if that happens it indicates that the threads have worn and are no longer suitable for gripping onto the regulator thread.
4. Fill 'er up!
The part we all know is coming, high pressure testing, but why are you putting water in my AIR bottle?!
Well, water wont compress anywhere near as much as air will, so, if there is a failure in the bottle under pressure, there won't be a massive purge of all the pressure that is being held. So that is a significant amount safer.
Our bottle gets filled via funnel to start (to make sure there is no air left inside) and then the hose is bolted on to the bottle via the regulator threads. At this point, i'm excited, a thick screen gets wheeled in-front of the bottle, and away we go, 4500 psi of water is loaded into the bottle. No problem, I've put that much air in there before, I'm confident.
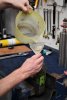
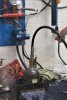
The bottle is checked for leaks, any sign of water making its way out of the bottle at this point would indicate an issue that would also happen with air.
The bottle is dry and the testing continues, it's at this point I start to get a little nervous, 6500 psi of water is loaded into the bottle. That is a lot of pressure!
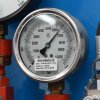
Fortunately for me, this bottle (like the majority of others) happily passes its testing, it is issued with another cycle of safety certificate (which takes this one up to its death date) and I am sent on my way.
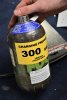
Many thanks to the guys over at Obsequio in Hampshire for spending the time with me, and for letting me jot down how it all happens.
Attachments
-
2.2 MB Views: 95
-
2 MB Views: 94